***** MAKE MPC GREAT AGAIN *****
MHEMPC Inc. is an Ontario, Canada based company, 705-919-2274,
email: sales@mhempc.com, dasbudd@gmail.com
Tutorial on MHEMPC here, read the tutorial first. Download and explore MHEMPC, download the zip file here. Use 7zip
- After automation we run the plant and do a performance test on the plant to prove all guarantees by the plant technology supplier.
- Then comes the tuning of the plant automation.
- We first tune the PIDs, 70% of profits from tuning.
- To break interaction among PIDs we put MPCs.
- Many plants do not need any MPC, well-tuned PIDs are good enough to stay optimal. Once PIDs become good, wait for 3 years to decide MPC.
- We at MHEMPC Inc., can carry out all post-automation activities, make PIDs run healthy, keep them healthy, and our MPC if required.
- Tuning automation is "not automation".
- MHEMPC is not an approximate algorithm, unlike every other MPCs.
- MHEMPC needs well-tuned balanced PIDs, so that they receive PID setpoints and change the plant.
Written in MFC/C++, Blazor/ASP.net. Since C# used in Blazor version is exposing internal database structure to hackers, it sits on a different webserver and thus no hacker entry to MHEMPC server. It will assist machine learning enthusiasts to directly use any math routine ranging from R to ExtremeOptimization to satisfy their needs. Tutorial pdf file of part 2 will contain a step by step method of how-to use ExtremeOptimization on ASP.net. MFC/C++ version is also configurable to pick and drop watch variables. Blazor/ASP.net architecture can be reused in supply-chain management of petroleum products that can sit on a public internet connecting distribution centers. Also note that MFC/C++ and Blazor/ASP.net software can also run on ARM64. Single developer (ie me) makes short development time, fault free and correct development, reducing price of delivery. Just like Java and every other bytecode, C# can be reverse engineered, a cyber-security risk, but there are plans, like a Golang server.
___________________________________________________________________________________________________________________
MHEMPC is guaranteed to be error-free, written by one person, following all software development principles.
Model Predictive Controllers(MPCs) are applied to all continuous Chemical Processes like Refineries, Petrochemical, Pharmaceutical, and many more. They keep the plant on optimal path of operation against ever changing feed quality, cost and specification of products and minimize operating costs, quality giveaways, also improving on stability, emissions and equipment life.
MHEMPC is the only state-of-the-art fully nonlinear MPC, runs in <3 seconds/cycle for a 7X5 system.
MHEMPC design can also use linear plant models ( same as other existing MPCs), both state space and time horizon models with dead time. Internal optimizer still remains same with nonlinear objective function and linear/nonlinear constraints. All types of tuning parameters like move suppression, CV reference trajectory exist simultaneously. Additional tuning parameter 'MV trajectory' makes aggressiveness adjustments.
MHEMPC uses the full computing potential of modern computers, modern C++ compilers and modern math. This MPC is for process optimization that meets process stability and optimality requirements much more effectively than all existing commercial MPCs. Objective function of MHEMPC can accept MV setpoints(IRV) from any external steady-state optimizer.
MHEMPC shall be able to replace many existing dysfunctional MPCs, by giving all good features individually existing in each of them and many previously non-existent features. Avoidance of 'continue-tuning forever as a full-time job' of failing MPCs and maintenance costs justifies such replacement projects. A single i7 computer(4 cores) can host 2 MHEMPCs under the same license. If more MHEMPCs are needed, a Xeon/EPYC processor can go upto 48 cores, 24 MHEMPCs can hosted at no additional price and some server motherboards do support 4 Xeon CPUs.
License price of MHEMPC is fixed per motherboard. If your refinery processes 100,000 bpsd crude, license price is US$100,000 per motherboard. Many MHEMPCs can be hosted on one motherboard, talking to several DCS.
MHEMPC is designed to give all the true benefits from an MPC, unlike existing faulty ones, so please do not waste time and further investment on trying to fix them. Make a move to MHEMPC now.
Simulation plant has the option of up to 7 independent MPCs (one byte to keep controllers' statuses). Collaboration between MPCs will be permitted, like cascading MPCs. Technology used are Windows 10, Visual C++, multithreading, mutex, in-memory real-time persistent data, Win32, system services etc. Memory-mapped file is extensively used. For those who used VAX/VMS global common like SETCON, even with 10MB hard-disk space we could hold real-time data of an FCC for a month.
Process data are not relational, just linear arrays of tuples.
Electronic instruments, connected to a DCS is used by operators to manually change plant settings. When the DCS is connected to a Windows computer, MHEMPC can calculate the same settings and download the values to plant. A data communication software is required for input/output with the DCS for closed loop implementation of MHEMPC. This software can be bought from the DCS vendor or OPC venders. If a Windows computer is already connected for MIS purposes, this may already be existing. Just write a program in C/C++/C# and test I/O on a dummy tag on DCS before calling.
No internet connection required , so cyber-security issues do not exist.
1. No MPC can reduce manpower requirement of the operation, an MPC just improves profit, only if properly working. When spikes in temperature is reduced, thermal shocks to the equipment is low.
2. Cyber security issues do not arise. It is not connected to internet, no username/password, no JSON, no TCP/IP.
3. A new Gresghorin circle based stability, unhackable substitute to RSA encryption developed ( unpublished).
4. Full view of internal variables as tuning aid, is coming up as a part 2 of demo software.
5. Writing code for someone else is easy, you just pass the tests. Finding bug in someone else's code is not easy, hence single developer.
MHE is Moving Horizon Estimation
- Chemical engineers need not know Instrumentation or Computer Science to implement MHEMPC, just C/C++.
- Page motivation describes benefits from this product and page description describes progress done so far.
- MHEMPC demo(x64). Documentation files added too. Need 7zip software to extract C.7z. Contains Simulation
- Demo version 2 equipped with a file based historian trend. This can build multiple tuning scenarios.
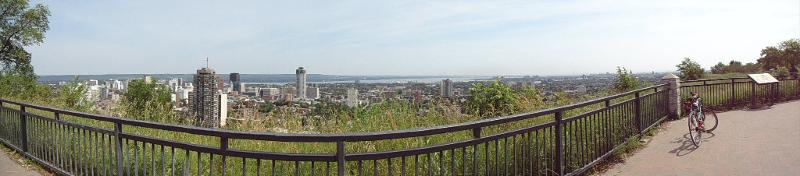
Next software project: Supply-Chain for chemical process industry... (without using RSA cryptography, not based on prime numbers and not published). Site-wide "Asset Management" is a subset of this, useful for turnaround planning and scheduling.
Reliable in performance, not hackable as the "internal protocols" are never published.
- Refineries use supply-chain for internal management.
- Crude receipt to gasoline stations too.
- Existing systems use heavy 3rd party software and Software integration is overdone.
- No heavy-duty servers, no RDBMS, just in-memoryDB.
- Single executable software to replace component based design, improving speed, reducing cost. (no DCOM, no CORBA, no XML/JSON, no JavaScript)
- Every other manufacturing uses supply-chain too.
- Not seeking any investor. Many base C++ components are already working at MHEMPC.